
transforming containers into self-sufficient housing units
Increasingly populated cities, skyrocketing real estate prices, ecology and climate change… all these factors make many people look for alternative forms of housing. One of such solutions are containers. Formerly associated with the transport of goods, today they are increasingly used as a material for construction houses, apartments or offices.
The potential for transforming containers into self-sufficient living units is enormous. Thanks to their modular construction, they allow you to easily and quickly create houses of various sizes and configurations. One of the most important aspects of using containers is their ecology. They are made of materials that can be easily recovered and recycled, which translates into less consumption of natural resources. In addition, the use of modern technological solutions in the construction of containers allows for reducing energy and water consumption, which in turn has a positive impact on the natural environment.
First, the economic benefits
It is no secret that the prices of apartments and houses are currently very high, and additionally financing in the form of a loan is unstable. Therefore, the first benefit, or rather a set of benefits of transforming containers into residential premises, are the economic aspects.
Primarily building of such an object is much cheaper than in the case of a traditional house. Cost container it is much lower than the construction of any other building from scratch. What else? Containers are readily available and can be delivered quickly to the construction site, reducing construction time and labor costs. Importantly, the modules are fully manufactured in the factory and then delivered to the site as ready-to-assemble elements. Also thanks to this, the total price of container buildings is attractive compared to other solutions.
Habitable containers they are also very flexible. In the case of traditional construction, e.g. brick construction, erecting the final version of the house is a long-term, or even "lifelong" solution. In the case of modular construction, adding additional elements is simple, quick and inexpensive. This means that you can change your requirements and needs at any time, without high costs and complications.
Secondly, short implementation time
Containers can be an alternative to classic construction, because the process of transforming them into self-sufficient housing units is much shorter than erecting a "normal" building. For example, the construction of a house or a multi-family building usually takes from 1,5 to 2 or even 3 years, which can be burdensome when you have to rent an apartment during this time. In the case of container buildings, everything takes much less time, even just a few weeks or days when it comes to small ones houses. It usually takes the most time to adapt the interior layout to the needs and expectations of the investor.
The "building" process at the destination is very short. It is enough to put the foundation from ready-made foundation blocks and adjust the electrical and water installations. The containers are then placed in the indicated place using a crane or HDS, which takes several to several dozen minutes. With larger objects, consisting of several or several dozen containers, the process takes correspondingly longer, but still much shorter than in the case of a traditional brick building.
Thirdly, durability for years
When looking for alternative forms of housing or a house, many people consider objects containerbut has concerns about the quality and durability of such buildings. They are often associated with "blankets" used as garages or storerooms on the plot. Modern containers, however, are a much higher quality solution, made of components with appropriate durability.
The strength of the containers also results from the fact that individual elements are manufactured in production halls in controlled conditions with the use of professional equipment and in compliance with construction standards. This minimizes the risk of errors. The assembly of doors or windows in the factory guarantees greater precision and is subject to meticulous quality control. Containers are delivered with complete electrical, plumbing and heating installations made by experienced professionals.
Another issue that is often raised is: insulation container buildings. Just like any other residential premises, they must ensure thermal comfort in winter. By choosing a product from a reputable manufacturer, you can be sure that container it is well insulated and soundproofed. Mineral wool and a vapor barrier foil are used for this purpose.
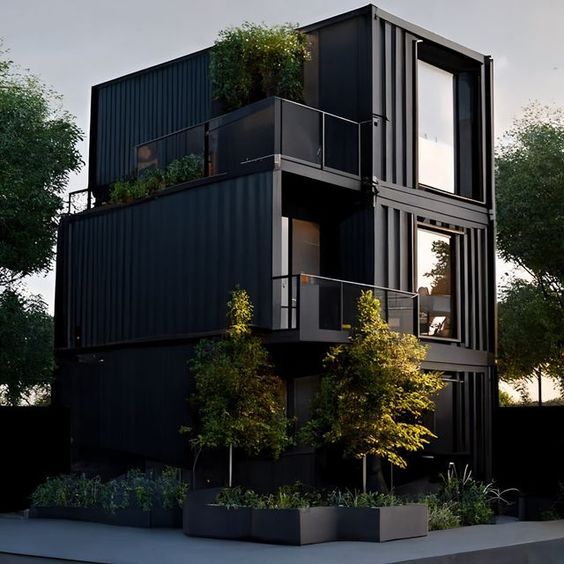
Transforming containers into self-sufficient living units
Stages of transforming a container into a self-sufficient living unit
The construction of a residential building using containers is not complicated, but it is worth knowing what stages await every investor. Each of these steps is important and cannot be omitted, but when we support the help of an experienced manufacturer, their implementation will be simple and quick.
-
Projects
The first step is to plan the living space. At this stage, you need to plan the layout of the rooms, select the equipment and develop an installation plan. The basis is to decide on the target size of the building. Next, you should design the functional layout and style of the interior, taking into account issues such as:
- number of container-modules to create sun,
- size of individual modules,
- functional purpose of individual rooms (e.g. number of bedrooms or bathrooms),
- setting containers on the plot and in relation to each other,
- arrangement of doors and windows.
It is worth using the help of experts, such as an architect or designer employed by the manufacturer, to make the house functional and meet safety requirements.
The modular structure of the containers allows for a wide adjustment of the equipment and the functional layout of the interior to the needs of each investor. IN container you can create a studio apartment, which consists of a bedroom, a kitchenette and a bathroom. By combining several objects, you can design a house over 100 meters high.
Buying a container from an experienced manufacturer gives you the opportunity to adjust the size and number of windows, add partition walls or expand the sanitary zone, e.g. with an additional toilet.
-
Formalities and plot preparation
One of the main advantages of container houses is the possibility of erecting them without unnecessary formalities. Manufacturers often present them as residential buildings, for which you do not need to obtain a permit. In some cases, this is true, but it must be remembered that it depends on many factors that affect the formal requirements. Before starting construction, it is necessary to carefully analyze the situation, because the law construction in Poland is complicated. On the websites of companies selling containers, you can sometimes come across simplified information on regulations, so it is worth using the services of experienced manufacturers who have full knowledge in this area. Experts from such a company will help in the implementation of the investment in accordance with the law.
During the formalities, it is worth focusing on the proper preparation of the plot on which the container building is to be erected. Work in this area mainly includes clearing and leveling the area. This is very important because the residential containers are placed on a small foundation, so proper leveling of the ground is crucial. The construction of the foundation will vary depending on the ground conditions. It is worth taking advantage of the manufacturer's opinion, because the requirements for the base of the house will also depend on the construction of the containers and the design of the entire facility, such as whether it will be a one-story or multi-storey building.
-
Installation of installations, including ecological solutions
Installation of the installation during the construction of a residential unit from a container is another key element of the process. At this stage, special attention should be paid to the selection of appropriate solutions that will make the use of the facility comfortable, and at the same time to minimize the selected solutions' impact on the natural environment.
W containers many innovative, ecological solutions can be used to save energy. One of them is the installation of photovoltaic panels that obtain electricity from solar radiation. Thanks to this solution, it is possible to achieve energy self-sufficiency. It is worth remembering that the most common form of heating container facilities are installations based on electric heaters. Therefore, obtaining electricity from renewable sources is particularly important.
At this stage of the project, water and sanitary installations are also an important element. A properly designed bathroom, toilet and kitchen are crucial for everyday living comfort.
-
Installation on the plot
This is the shortest stage in creating a residential unit from a container. Depending on the project, it proceeds in different ways. In the case of a single-module house, the whole operation takes only a moment. Such buildings are erected in the indicated place using a crane or HDS, and it takes literally several minutes. Then it remains only to connect electricity and water. In the case of a project consisting of several or a dozen or so modules, combining them takes a bit more time and requires specialist skills. Therefore, it is worth leaving this operation to an experienced manufacturer who will supervise the entire process of assembling, stacking and connecting containers.
-
Interior fittings
After installation, all that remains is to finish the interior. This stage is very important because it affects the final comfort and appearance of the living space. This includes laying the selected floor, painting the walls and ceilings, and arranging the kitchen and bathroom, just like in a traditional apartment. Unlike buildings using traditional technology, buildings made of containers do not need external finishing. Ready-made modules are delivered in a previously selected finish, most often in the form of walls made of painted sheet metal or with a wooden facade. The next step in this process is to place equipment items such as furniture or household appliances. It is important to choose elements that have low power consumption and at the same time provide high efficiency.
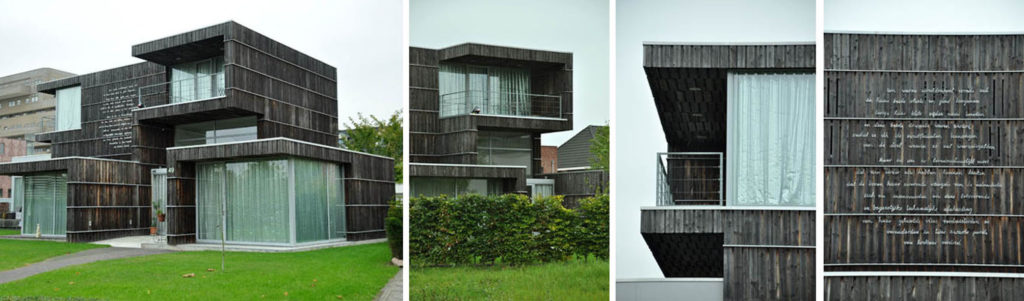
Designed by W. Sobek, this four-story building residential with an area of 200 m2, it was harmoniously integrated into an area densely covered with trees on a steep slope. Transparent walls perfectly integrate the building with the surroundings, creating a natural landscape as a background for the daily life of the residents. The structure is based on a light steel structure with glass elements on the façade. The modular characteristics of all components of the facility facilitate the process of prefabrication, assembly and disassembly, which results in shortening the construction time and enables full processing of the building in the future. Glass facade panels, filled with gas, effectively protect against overheating and frost, while the possibility of opening some window panels guarantees natural air circulation in the building. In addition, the residence has been equipped with forty-six solar panels and a heat pump, which ensures its energy independence. The structure of the building consists of a four-storey grid made of steel elements, 11,2 m high. All structural connections were designed as tongue-and-groove joints or using bolts and carefully designed holes, which accelerated the assembly process (4 days), facilitated disassembly and allowed to minimize the amount of material used. In line with the reversibility concept, all building materials used, such as steel, aluminium, glass and wood, can be recycled.
An interesting alternative
Converting containers into self-sufficient living units is a worthwhile alternative to traditional construction and is becoming increasingly popular in the construction market. With the use of containers, you can quickly and inexpensively (and also ecologically) build your own place of residence.
In order to carry out the investment without any problems, it is worth getting acquainted with the formal requirements and using the support of experienced producers. Thanks to this, you can be sure that the project will be implemented in accordance with quality and safety standards.